
Centrifugal Casting
The centrifugal casting method is the method to produce pipes by pouring molten metal into a rapidly spinning cylindrical mold in which centrifugal force from the rotation exerts pressure on the molten metal. In 1952, Kubota developed its first centrifugal casting technology for steel. Since establishing a framework for industrial-scale mass production, Kubota has steadily supplied high-performance, high-quality steel castings for industrial equipment.
Core Technologies
Advanced centrifugal casting technology produces high-quality castings
Advantages of Centrifugal Casting
Directional solidification, starting from the outer face in contact with the metal mold, realizes a sound cast metal quality, free of cavity and inclusions. The centrifugal force produces a hollow cylindrical product with no wall thickness variations. Another advantage of the centrifugal casting method is that residual stress after casting is minimized because there is nothing to disturb solidification shrinkage.
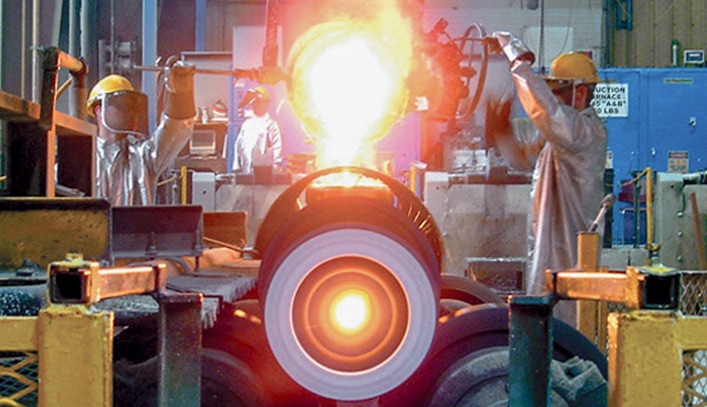
Horizontal Centrifugal Casting
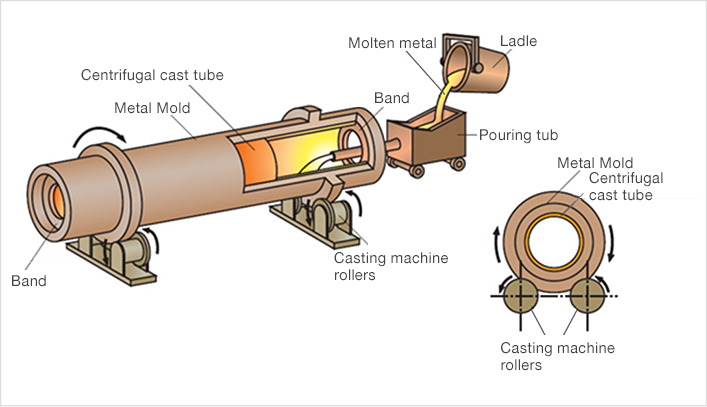
Dual Layer Casting
Advantages of Dual-layer Centrifugal Casting Pipes
The outer and inner layers are metallurgically bonded into a completely integrated structure.
A wide choice of outer and inner layer combinations is available through perfectly controlling the molten metal temperature and optimally configuring casting conditions.
Products can be designed to have a variety of features by altering the inner and outer layers.
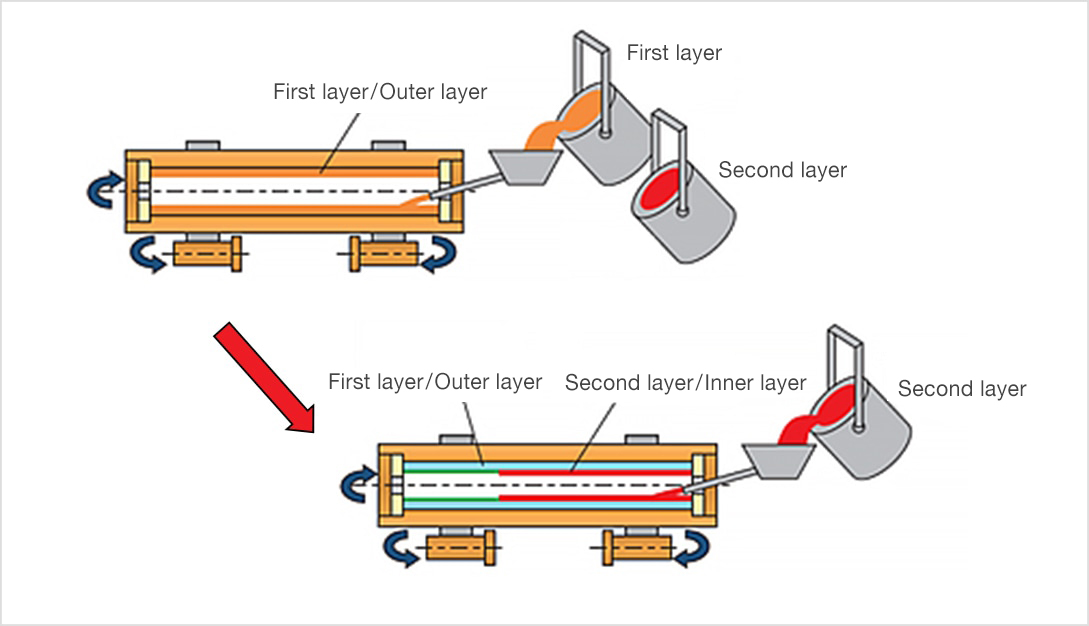
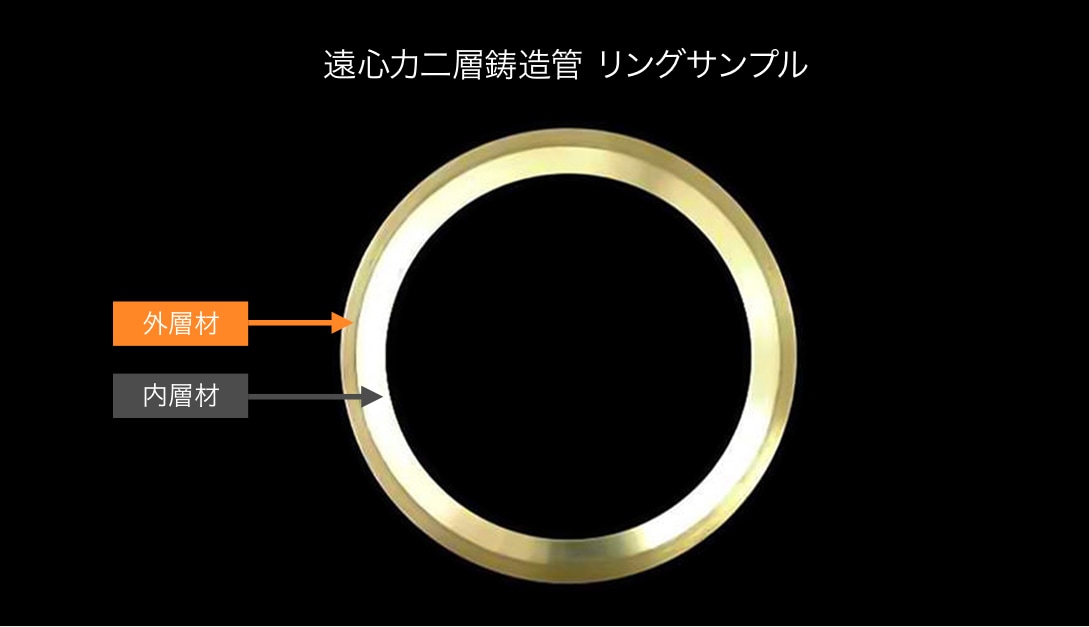
Multi-Layer Casting
Kubota's Centrifugally Cast Composite Rolls
- Kubota chose a centrifugal casting method for manufacturing rolling-mill rolls in 1961, earlier than any other manufacturer worldwide.
*Rolling-mill Rolls series was discontinued in 2022 - In 1991, Kubota began producing the world's first centrifugal cast composite rolls with an outer layer made of a high-speed tool steel material with high resistance to wear and surface-roughening performance. An intermediate layer based on our proprietary technology is provided between the outer layer and the core to improve the boundary strength.
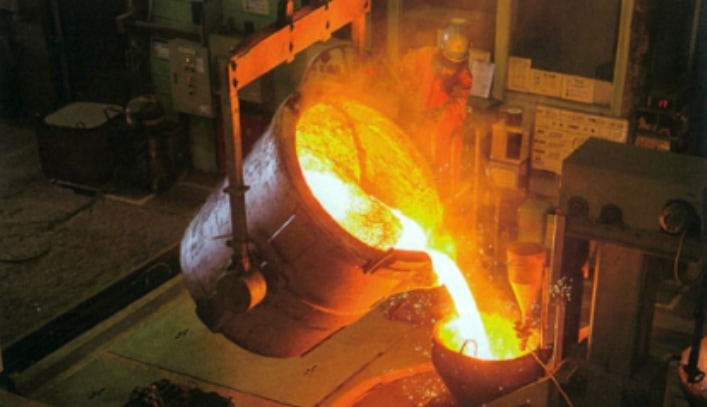
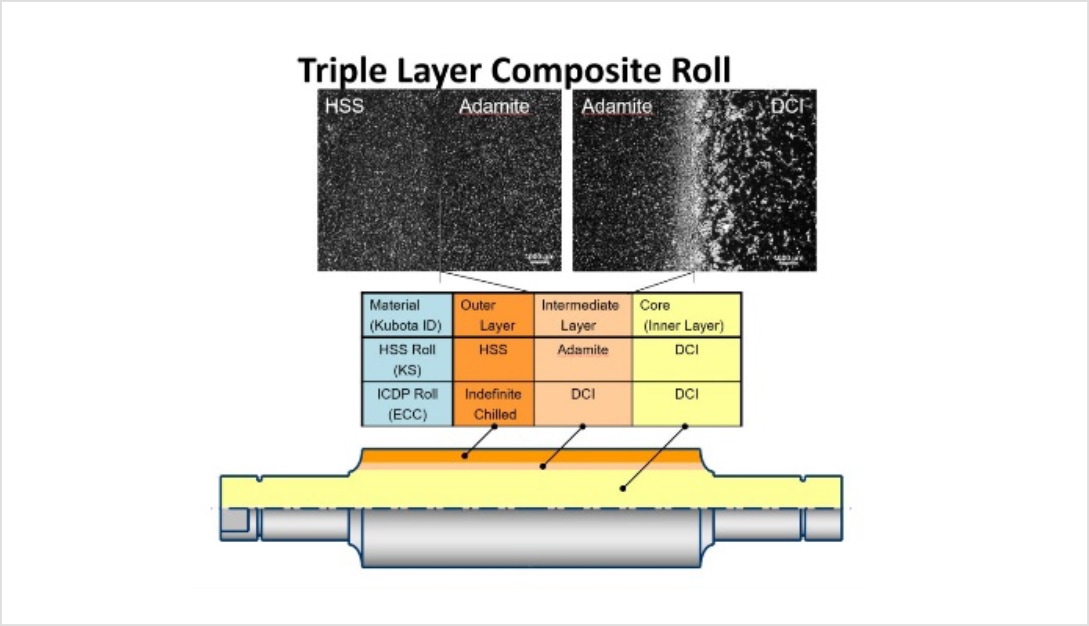
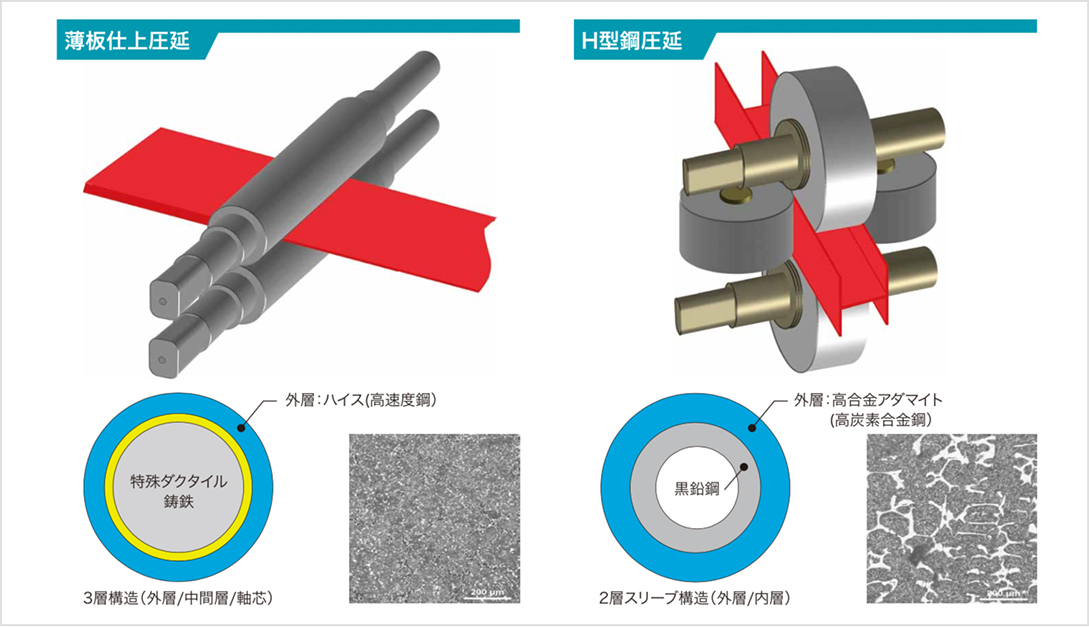
Related Products
Cracking Tubes (Cracking Coils)
Cracking tubes are used in the manufacturing processes for ethylene and propylene, which are the raw materials of petrochemical products.
Reformer Tubes
Heat-resistant cast steel reformer tubes are employed in such processes as oil refining, methanol manufacture, and ammonia synthesis.
Industrial Steel Castings
We have established an organization to cover all stages from research through manufacturing and inspection of alloy materials for industrial equipment to be used in extreme environments. By using our proprietary casting process technologies, we are able to offer a wide range of products that are highly resistant to heat, corrosion and abrasion for different service environments and to meet different property requirements.
Related Technology
Materials Development
Materials which demonstrate ideal characteristics across a wide range of industrial fields in a variety of environments. Kubota develops and offers materials with the most suitable properties to meet customer needs, based on many years of experience, unique technologies, and solid success records.
Related Industries
Petrochemicals & Petroleum Refining
We develop long-life materials that possess superior heat resistance, corrosion resistance, and creep characteristics needed to withstand severe environments in industrial furnaces. We also offer high-performance piping products with tailored interior shapes or interior surface modifications using our proprietary technologies to improve the efficiency and performance of industrial furnaces.
Automobile Industry
We process a wide variety of materials, from steel to plastics, using a range of technologies. Kubota's TXAX is a brake pad friction material that has less impact on the environment, favored by many users both within and outside of Japan.
Contact Us
To inquire about a product, service, maintenance, or any other matter, please contact your nearest Kubota location directly by phone or contact us by email. Before making an inquiry, we recommend that you check out our customer support information, including FAQs, as you might be able to find the answer to your question more quickly there.