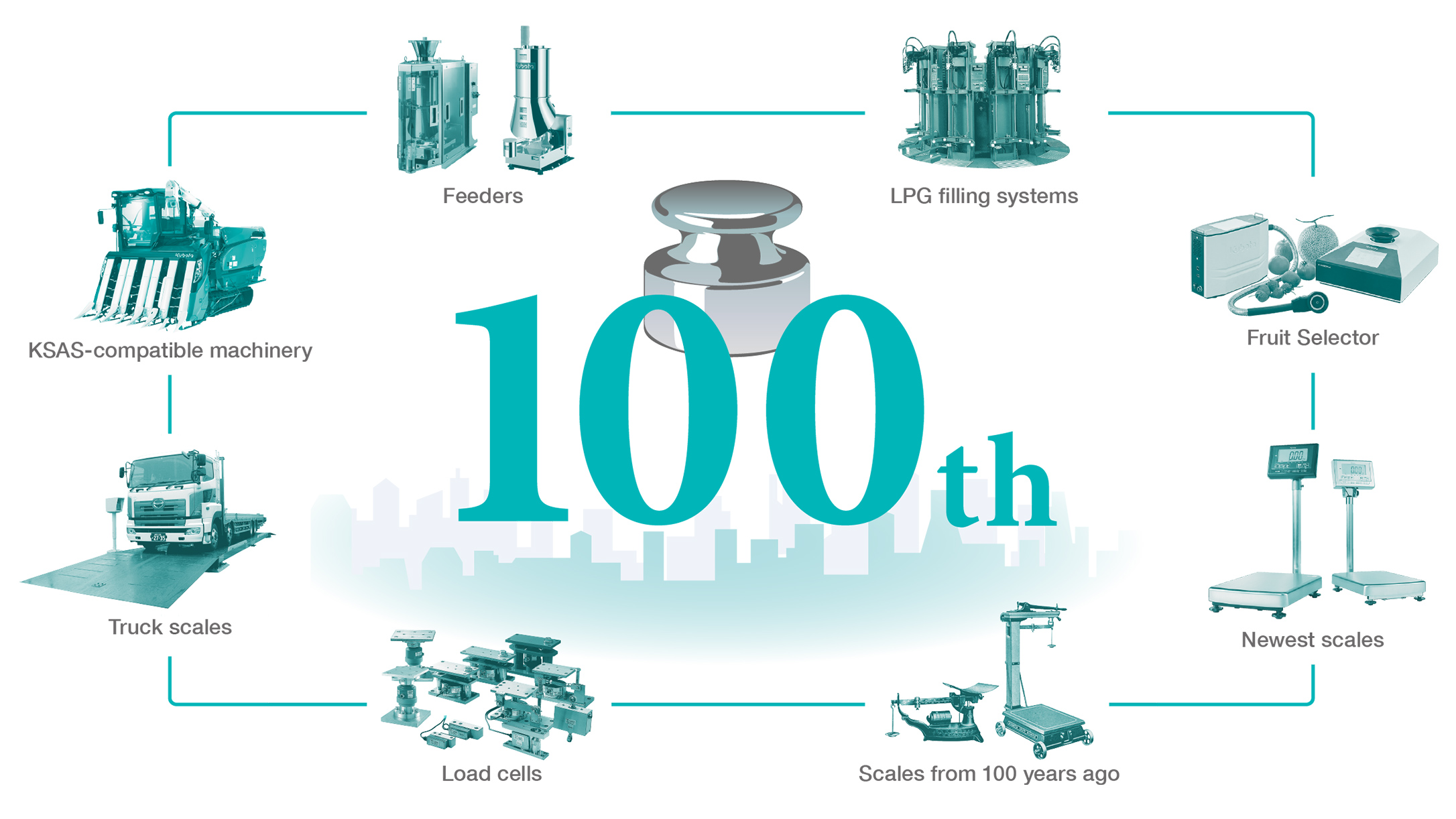
The Nobel Prize in Physics 2023 was awarded for experimental methods that generate attosecond pulses of light. An attosecond is an extremely short unit of time, equal to one quintillionth of a second, and attosecond pulses are the optical signals that enable the measurement of this unit. These pulses make it possible to measure the movement of electrons, which could not have been captured before due to their extremely fast speeds. A substance’s structure, function, and reactions are determined by the state of its electrons. There are hopes that measuring the movement of these electrons will reveal unknown properties in substances, and that controlling the movement of electrons will lead to the creation of new substances, bringing major developments to a wide range of fields from healthcare and drug discovery to solar cells, photocatalysts, ultra-fast electronic devices, and new materials. Measurement has always been the foundation of science, providing the cornerstone for pioneering new technologies and fostering industrial growth.
Kubota has been supporting the development of society and industry through products and technologies related to weighing and measuring for 100 years, since the company began manufacturing mechanical scales in 1924. We talked with Koichi Segawa, Technical Fellow at the Precision Equipment Business Unit, about the history of scales’ advancements and diversification as led by Kubota, and their future prospects.
How Scales have Evolved while Enabling Developments in Society and Industry
Scales are used to measure mass, but the ways they show us this mass have changed with the times. One unit of measurement called sho was used from the Nara period of Japanese history (710-794). This unit is based on square wooden boxes, and it is still used today for measuring rice. However, there were variations in this sho unit’s size depending on the time period and the region. It is believed that this resulted from feudal lords in different areas gradually increasing the size of the boxes so that they could collect as much rice as possible, since people paid their yearly taxes in rice back then. As areas of commerce expanded, a uniform standard became necessary. Over time, accurate measurements of lengths and weights would become the basis of production, sales, and most other social and industrial activities.
In 1921, the Japanese government revised the Law of Weights and Measures and unified measurement units to meters and kilograms. Kubota, which specialized in scales along with cast iron pipes and machinery since its founding, obtained a license to manufacture scales in 1924, and began making mechanical scales, including steelyard balances with upper pans and platform scales.
The principles of mechanical scales can be categorized in two types: balance scales and spring scales. A balance scale compares two objects to measure weight, while a spring scale converts the extension of a spring into mass to weigh an object. With the standardization of weight units aimed at rationalizing industry through the unification of industrial product standards, the use of scales as measuring equipment became more widespread throughout various fields. Kubota carefully studied each industry’s needs involving measurements and developed a variety of scales.
With the mass production and mass consumption that began following Japan’s postwar reconstruction period, needs for measurement increased even more. People wanted to be able to measure things faster and more efficiently. Kubota promoted the mechanization and computerization of scales and worked to provide solutions that combined accuracy with speed at advanced levels for various applications.
In the 1980s, scales using load cells became widely adopted. This type of cell is a sensor that converts the strain created when a load is applied to metal into an electrical signal. The weighing results from scales using load cells are displayed in easy-to-read digital numbers. Before this technology came along, people had to read finely-engraved markings on scales, taking time and making human error in readings inevitable. Load cell scales made it so that anyone could see the weight at a glance, bringing about revolutionary changes in society. Kubota developed load cell-equipped platform scales, truck scales, feeders (see below), and other technologies as it worked to popularize these products for both home and business use.
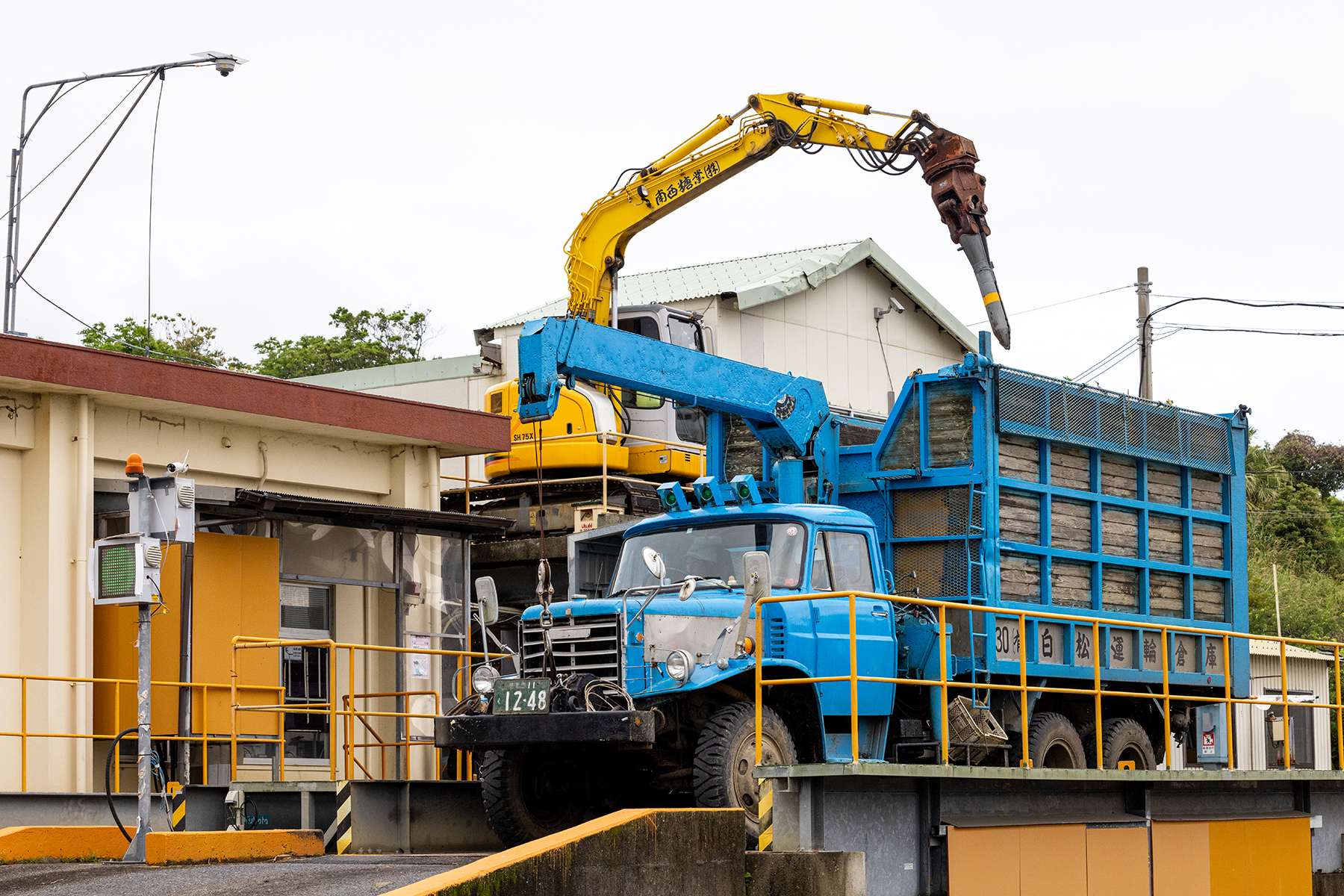
The next turning point was the adoption of digital load cells in the 2000s. Kubota was the first company in Japan to develop digital load cells and succeed in turning them into products. These cells provide direct output of digital signals, enabling highly accurate weighing that is resistant to noise. They are also equipped with temperature sensors to minimize the influence of environmental changes, enabling reliability when used outdoors and in other harsh environments. Along with improvements in maintainability, these cells have paved the way for the use of scales in a greater variety of workplaces.
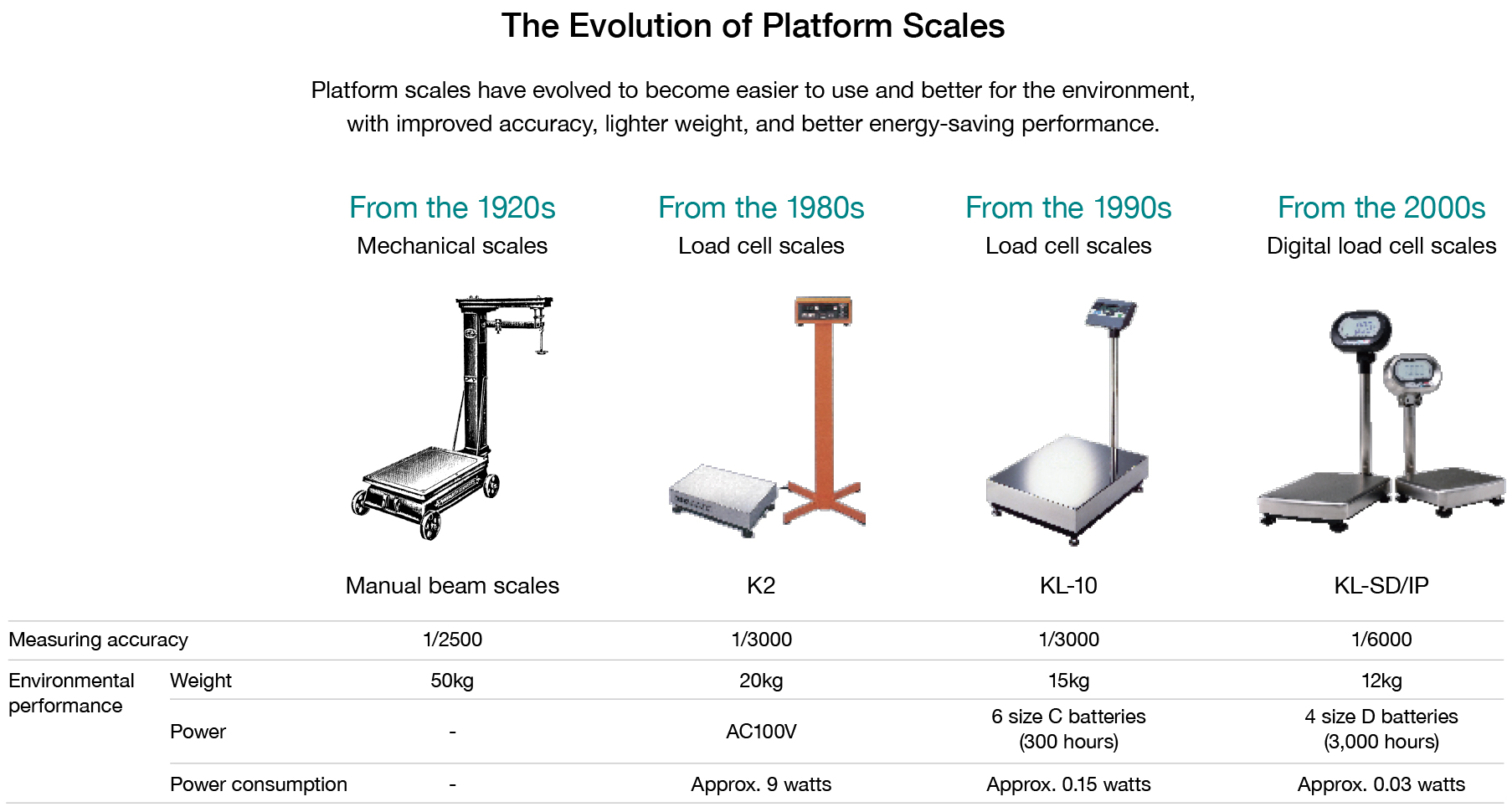
What is more, to support the manufacturing industry of Japan, Kubota has developed a large number of products that incorporate its measuring technologies. One of these is its gravimetric feeder. This instrument supplies raw materials in powder, grain, or liquid form to next processes in constant pre-set amounts. In recent years, high-performance resin materials have been utilized more and more as alternatives to metals in many industries, from automotive to home electronics, thanks to their light weight and ease of processing. These resins are made by mixing multiple raw materials, so their quality requires accuracy in the mixing process. Kubota has leveraged its advantages in developing its own load cells to provide chemical manufacturers and other companies with feeders that can handle various kinds of materials and applications. Feeders are the behind-the-scenes helpers of modern industry, and recent years have seen the emergence of models capable of handling a wide variety of raw materials. These feeders are now being exported to China and Southeast Asian countries.
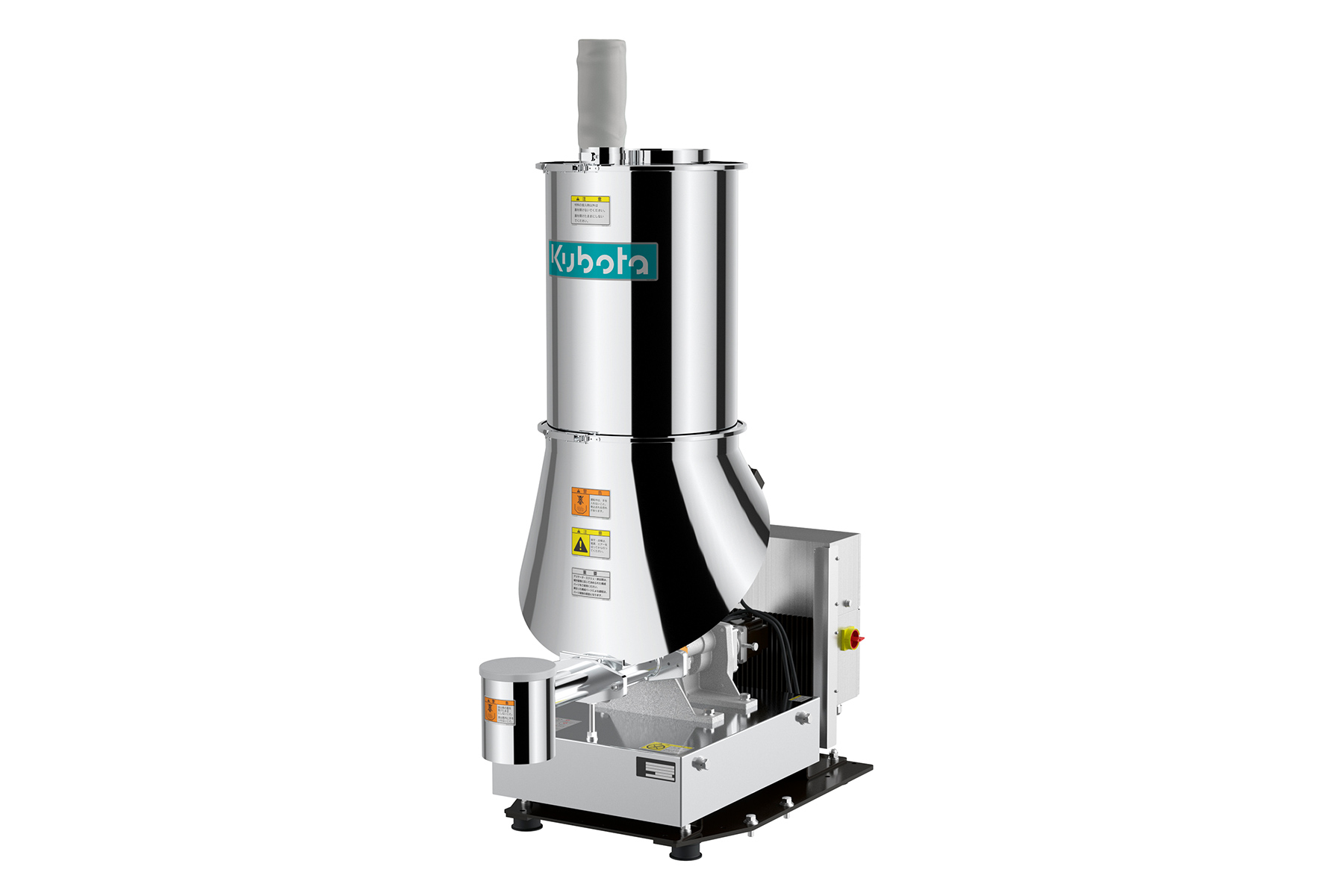
Digitization Leads to Diverse Applications, Enabling Measurement of Taste and Other Invisible Aspects
Measurement technologies have made great strides through changes over the last century. Koichi Segawa has been involved in the scale business since joining Kubota. “Combining light, images, and other measurement technologies, or sensors, with all kinds of weighing technologies has led to great advancements, such as the ability to measure the flavor of agricultural crops and other invisible things,” he says.
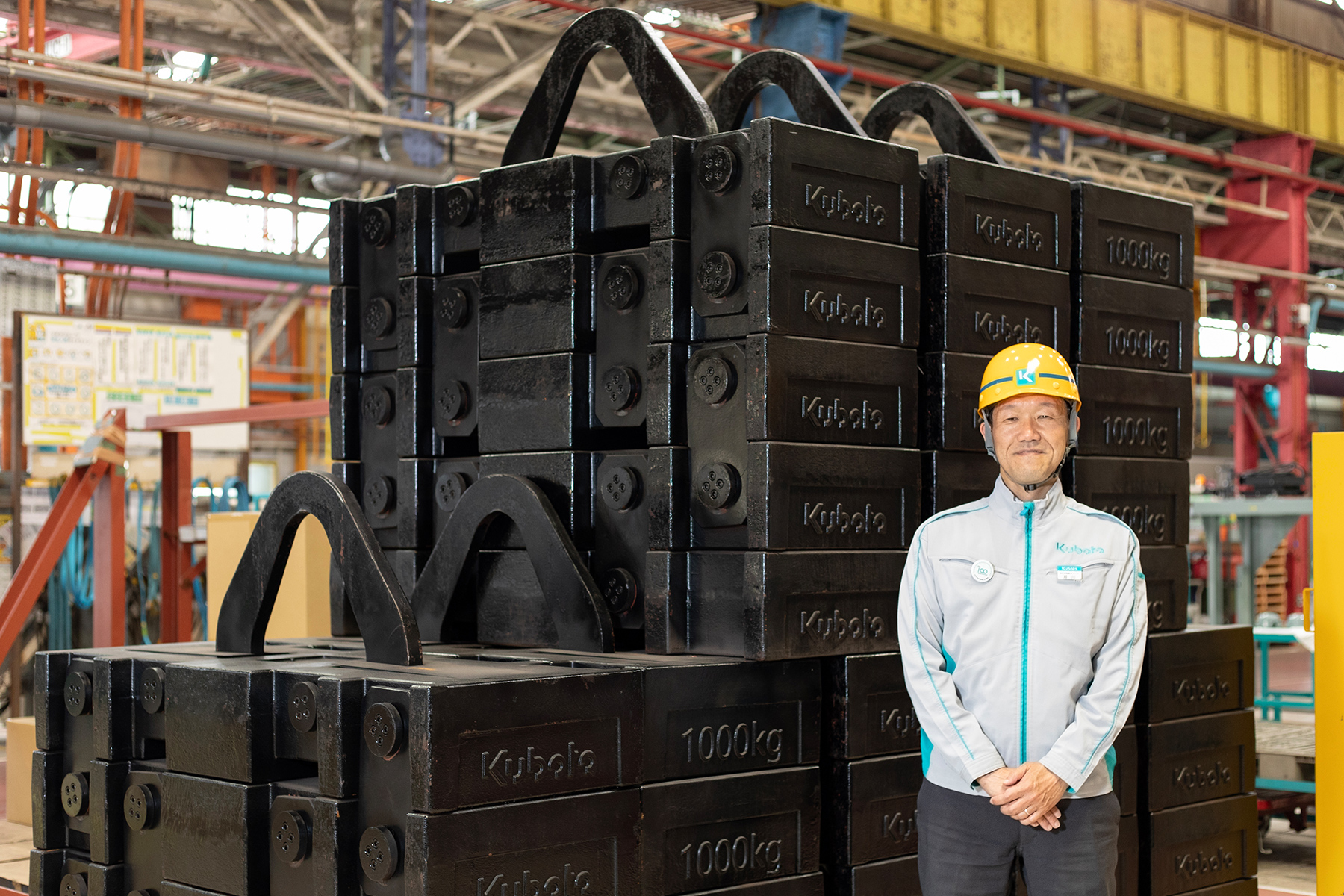
“For example, our Fruit Selector is a non-destructive sugar content measuring device that works by shining small amounts of light on fruits and vegetables to measure their sugar content without damaging them. It was developed to answer needs for selecting only the best-tasting items – that is, the ones with higher sugar content. This has helped to add greater value of agricultural products, such as applying a brand name to fruits and vegetables that meet or exceed a certain sugar content level.”
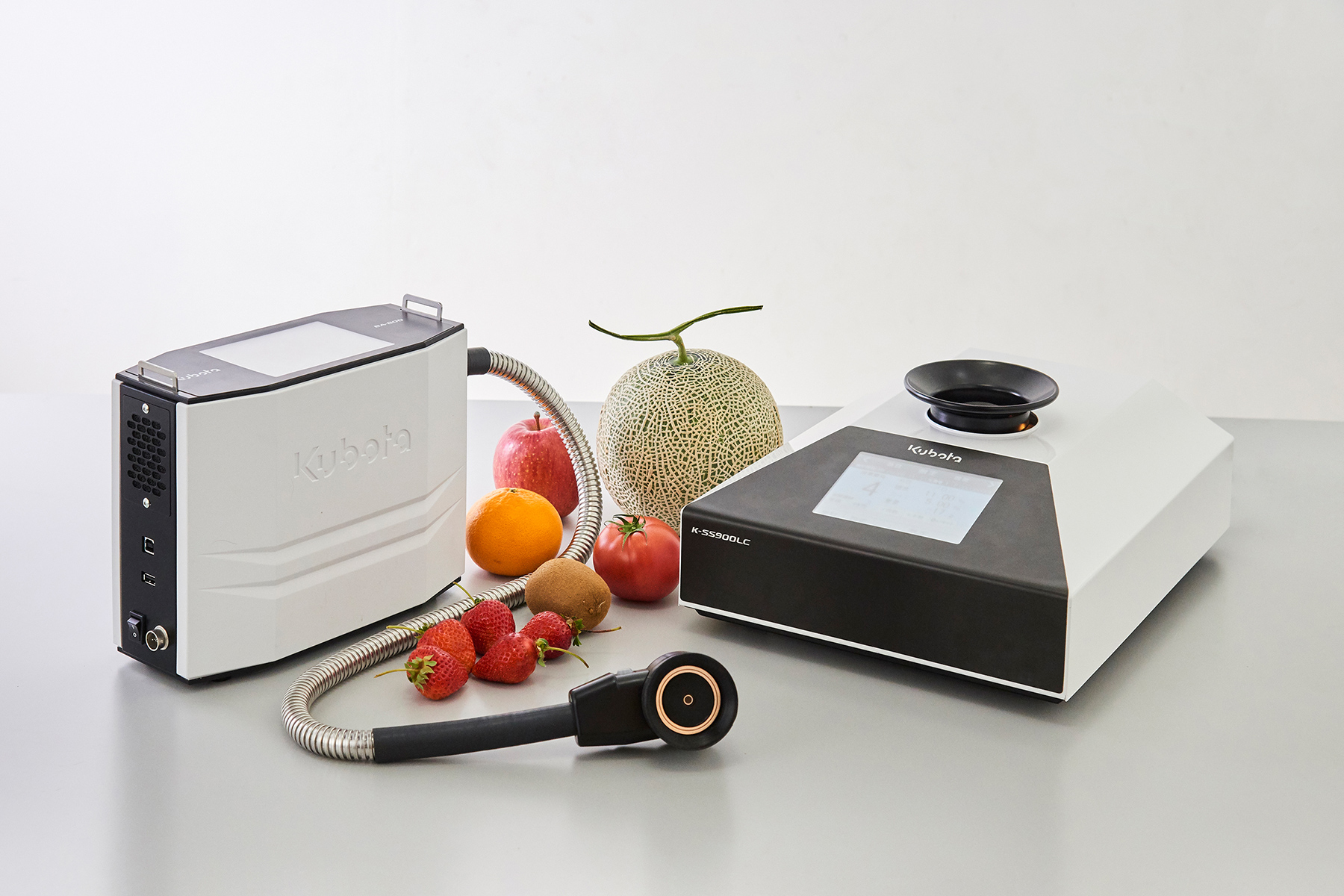
Scale technology combined with sensors is also being utilized in smart agriculture. The taste and yield sensors in the combine harvesters*1 compatible with KUBOTA Smart Agri System (KSAS), Kubota’s support system for farm management and services, can be used to measure the flavor and yields of rice.
The taste sensor irradiates the rough rice with near-infrared light, finds the wavelength of the transmitted light and converts it into a component value to measure the percentages of protein and moisture in the rice. These values in rice have a major impact on its taste, so measuring them can determine how good the rice will taste. On the other hand, the yield sensor is a sensor that applies the digital load cell. It is mounted on the bottom of the combine harvester’s grain tank and weighs the harvested rice to determine the yield.
- *1: Agricultural machinery with reaping, threshing, and sorting functions. It is mainly used for harvesting rice, wheat, and other such crops.
Linking Measurement Needs and “Seeds” to Generate New Value
As detailed above, scales and sensors can be used in ingenious ways to measure taste and other intangible aspects of things. One example is with trucks that carry waste products. If a truck packed with waste is weighed before and after it delivers its cargo to a disposal facility, the weight (mass) of the waste can determined, and this can be used to calculate CO2 gas emissions. This kind of clever thinking can enable measurement and visualization of various things. But in what areas can we expect to see an increase in measurement-related needs? “One of the best parts of the scale business is to find what the needs or challenges are, to explore solutions to those needs using our technologies as the ‘seeds,’ and to provide solutions to customers at a reasonable price,” says Segawa.
For example, the taste and yield sensors were developed as a result of the needs to add even greater value to KSAS, which is used to manage farm fields and work plans and can automatically generate work logs based on combine harvesters’ GPS data.
“Being involved in the agriculture and scale businesses is also an advantage for Kubota,” adds Segawa. “This synergy has been achieved through the passionate commitment of those working in both fields to create unique value by integrating these two areas. By using KSAS-compatible combine harvesters equipped with taste and yield sensors, farmers can get a detailed understanding of what areas in their fields produce the best-tasting rice and where the yields are higher. This information can be used for the following year’s fertilization plans and field improvements. Measurement can also prevent overuse of fertilizer, helping to reduce agriculture’s impact on the environment. We are currently involved in research to see how the taste sensor and Fruit Selector technologies can be applied to determining optimal harvest times.”
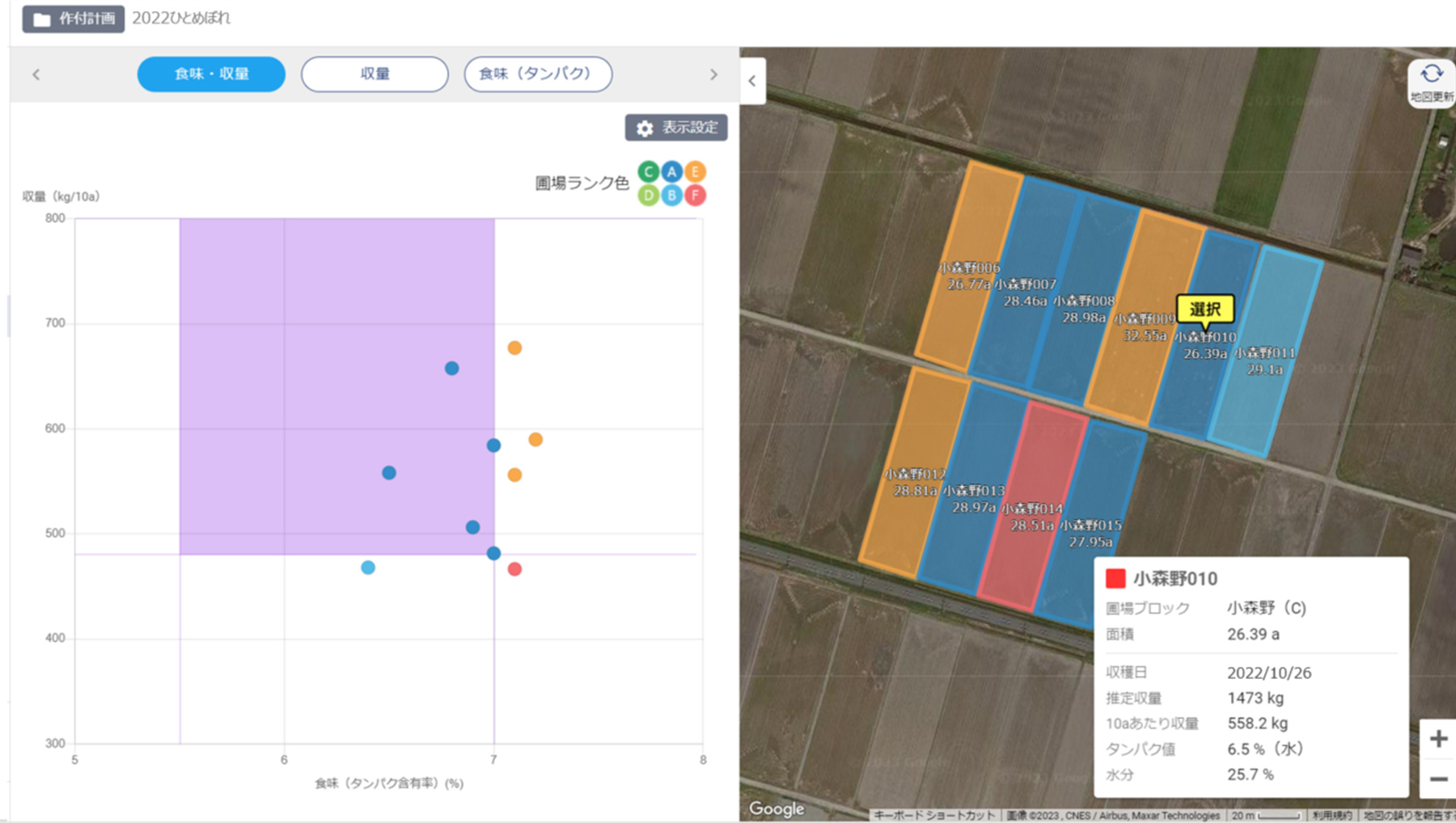
There may still be areas in which Kubota can generate new value through synergy between its scale business and other businesses. Kubota is also on the lookout for needs of customers outside the company. “We are always exploring various needs and applying trial and error to find ways to realize them,” says Segawa. Precision Equipment Business Unit technicians and sales representatives have begun training in “design thinking,” a thought process that attempts to solve unknown problems from customer viewpoints.
Creating New Forms of Measurement through Unyielding Tenacity
The scale business of Kubota celebrates 100 years in 2024. This business began with scales, which form the foundation of various industrial activities by measuring weight accurately. The importance of this is evident from their regulations through the law called the Measurement Act. Kubota strives each day to improve its measurement technologies in order to keep contributing to the future development of society and industry. One area of focus is the realization of a resource circulation society.
“We are continually working to improve the environmental performance of the products themselves. It is a rule in our development division that we must obtain our internal Eco-Product Certification*2 for redesigned models of products. Through environmental considerations in terms of continuing to make products with lighter weight, lower power consumption, and minimized use of harmful substances, we will contribute to the society of the future. And because long-lasting products also help to reduce environmental impact, we are focusing on evaluating their durability.”
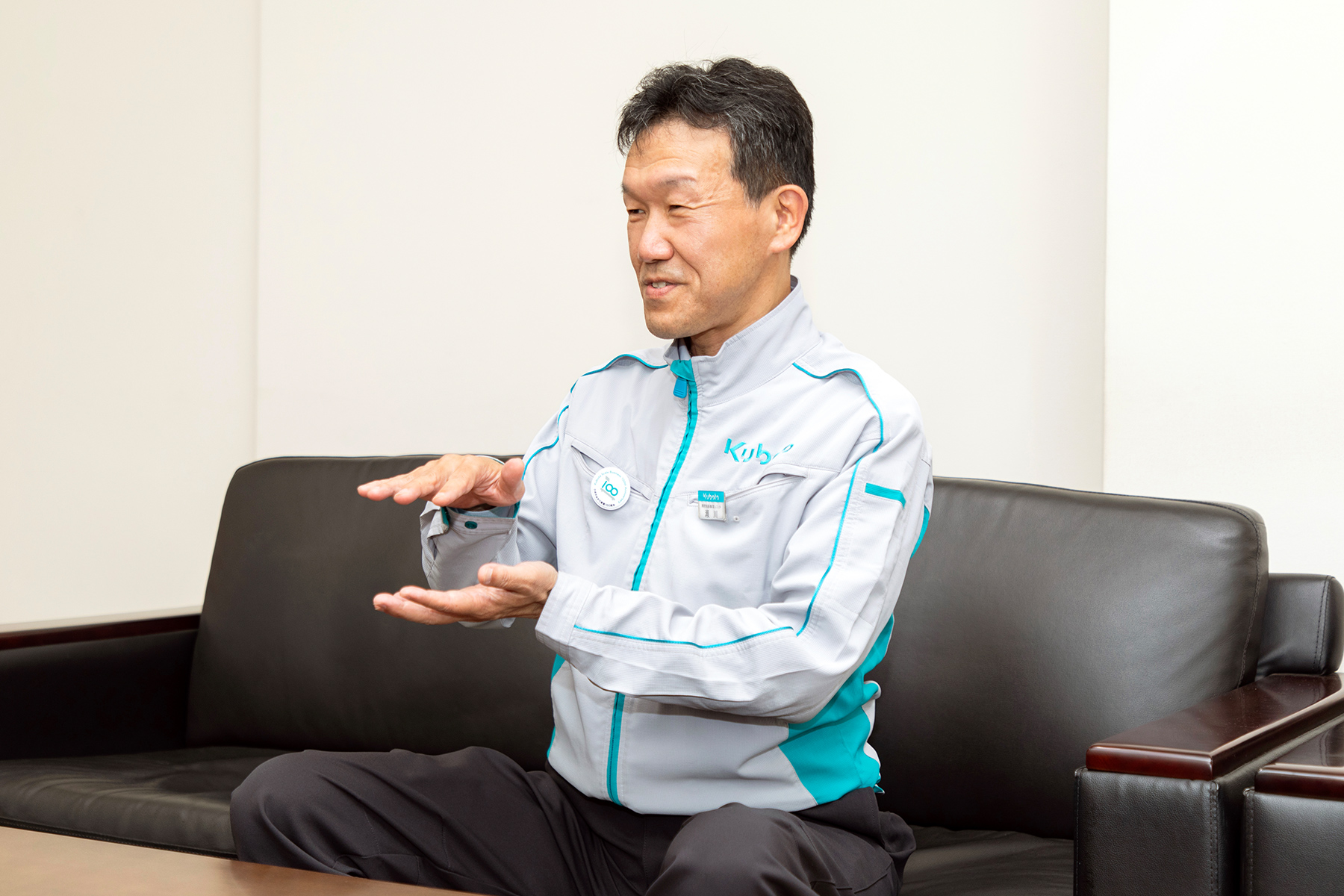
Just as digital load cells have been applied to a variety of products, the next move is to expand the range of applications for feeders.
“We currently provide feeders mainly to customers such as chemical companies that work with resins, but we have also learned that there is also demand for them in processes that continuously mix multiple raw materials in food and pharmaceutical production. Each of those areas has its own unique requirements and regulations, so we are continuing to look into ways to meet those.”
For this endeavor, one possibility is synergies with Brabender Technologie, which became a fully-owned subsidiary of Kubota in 2022. The Germany-based company is a global manufacturer of gravimetric feeders and provides feeders to a wide range of industries, including food and pharmaceuticals. Generating new value through a combination of the advantages and expertise of the two companies is one of the goals of the scale business.
Segawa also points out the resilience and tenacity of the employees at the scale business.
“I don’t think a person could do this work without those qualities. For example, brokers at fish markets use our scales to weigh seafood for loading and unloading, and if the weights are not correct, we will lose the trust of the fishermen. On the other hand, weighing accurately is a battle against errors. It is difficult to make sensors work in accordance with principles of detection, and sensor output may change with changes in environmental temperatures, which results in errors. When we are developing a new scale, we have to do trials many times, and there are often failures. Digitization may be advancing, but the world of measurement is still very much analog. In manufacturing and inspection processes as well, errors have to be kept within standard ranges in the various fields where scales are used, and this is something for which we have to keep up steady efforts on a daily basis. If employees get worn out from these failures and this work, we cannot reach the level we are striving for. Tenacity and resilience are the spirit for Kubota scales, and this goes back to the unyielding spirit of our founder, Gonshiro Kubota.”
- *2: An internal system to certify highly environmentally friendly products. The Kubota Group’s environmental management system evaluates products based on five basic criteria – Stop climate change, Work toward a recycling-based society, Conserve water resources, Control chemical substances, and Conserve biodiversity – and products that meet these internal criteria are certified as Eco-Products.