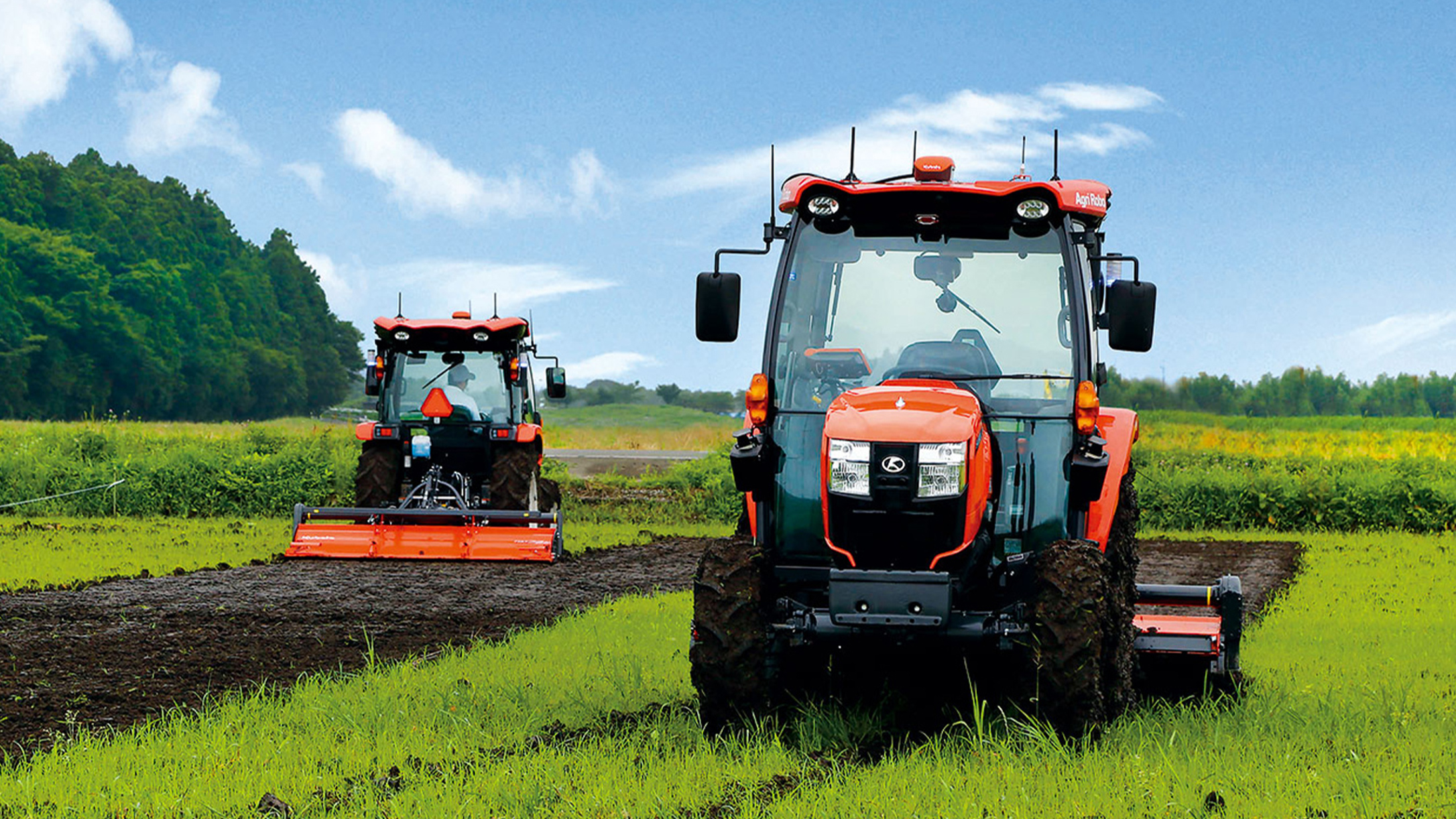
Cars that automatically brake when they sense danger. Drivers on public roads with their hands not touching the wheel. Maybe you’ve seen these kinds of commercials on TV.
However, automated driving is not just for cars. Research, development, and product design are now under way for tractors, rice-transplanters, combine harvesters, and other agricultural machinery that work on farms and in fields to make the machines autonomous and driverless. In this article, we will focus on Kubota’s technologies that make autonomous operation possible and unlock some of their mysteries. Research and development are progressing on self-driving farming machinery to make it completely autonomous, but how far have the technologies come that will help to solve the problems facing agriculture in Japan, including the aging population of farmers?
Unmanned Operation with Monitoring Has Been Put to Practical Use
As the figure below shows, Kubota’s roadmap of automatic and unmanned agricultural machinery has three steps. In addition to the rice-transplanters and tractors with keeping straight functions that correspond to Step 1, Kubota has launched tractors, combine harvesters, and rice-transplanters with automated and unmanned operation under monitoring by people, fulfilling Step 2. Kubota is now engaged in further research and development toward realizing the completely unmanned operation under remote monitoring in Step 3.
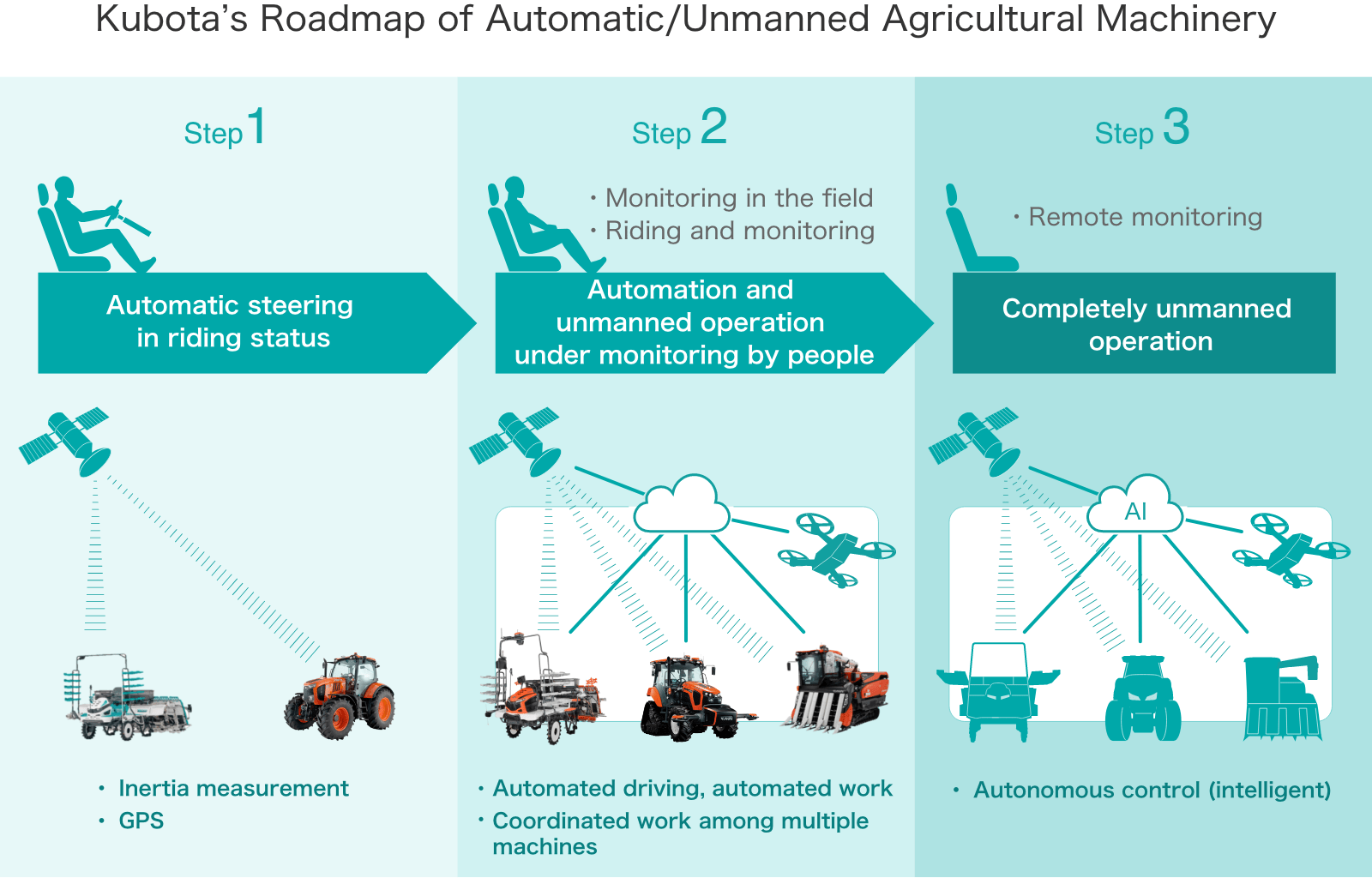
Although they are similar, automated driving for agricultural machinery requires different technologies than automated driving for cars. This is because of the differences in where they operate.
Conditions Specific to Automated Agricultural Machinery
Cars drive automatically using systems that recognize signs, traffic lights, road lines, and other markers, but farms and fields have no such markers. That is why self-driving agricultural machinery must rely on positioning information from satellites to determine routes.
In addition, cars generally drive on well-maintained roads, while agricultural machines work in fields with rolls and slopes. To efficiently plow uneven fields and fully harvest crops requires advanced vehicle control technology as well as the ability to cope with deviations in positioning information when the vehicle tilts.
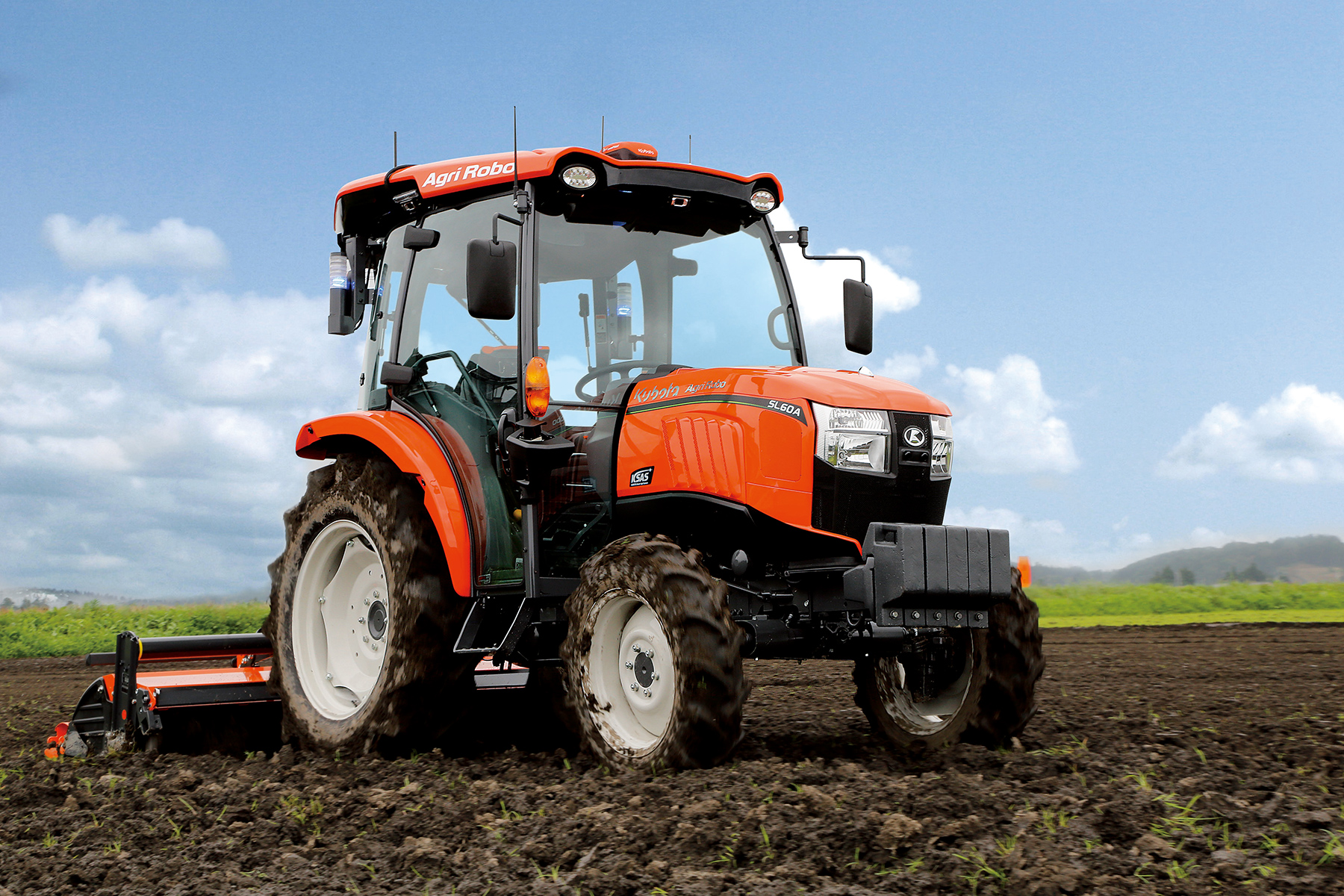
Of course, proper safety measures are also important. The system must prevent collisions by detecting surrounding obstacles and people while driving in areas without traffic signals. Meanwhile, sensor technologies are required to distinguish between crops and obstacles so that crops are not viewed as obstacles.
These are some of the reasons that self-driving agricultural machinery requires different kinds of sensor technologies and highly accurate positioning information than the ones used in automobiles. So, what kind of technologies are being used in Kubota’s products? The company’s automated agricultural machinery series includes Kubota's autonomous agricultural machinery, which features advanced functionality that achieves Step 2 in the roadmap above. Here we will introduce three examples of technologies in this product.
Kubota Autonomous Technology Combines High-Precision Automated Driving with Safety
The three technologies in this article are the RTK-GNSS unit, Surround View, and Human and Obstacle Detection System. These technologies enable the system to support the following features: autonomous operation by a single vehicle under human monitoring, cooperative operation by two vehicles with one operator using both unmanned and manned vehicles, and simultaneous operation of two machines (usually a tractor and an unmanned machine).
Exclusive RTK-GNSS Unit Enables Highly Accurate Positioning
GNSS is the name of a positioning system that uses multiple positioning satellites including the GPS that we use in our everyday lives. However, the use of only positioning satellites can result in errors of up to several meters due to satellite orbit deviations and other factors, making them unsuitable for agricultural work, which requires high degrees of precision. The Real-Time Kinematic (RTK) method is used to reduce these errors. It uses correction information from a base station on the ground to achieve greater accuracy in positioning.
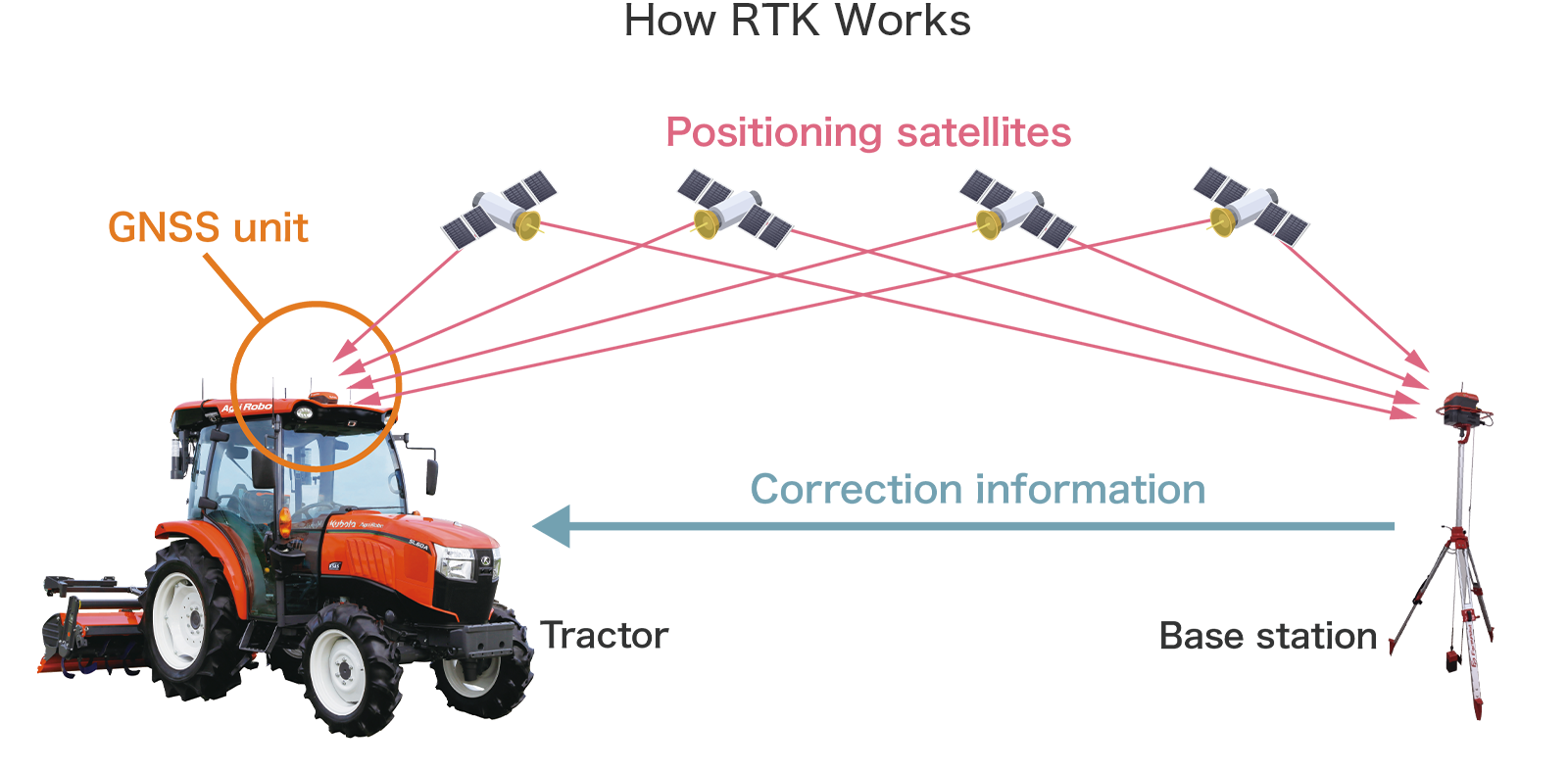
With the RTK method, distance information is sent simultaneously from positioning satellites to the GNSS unit on the top of the tractor and to a base station. The base station then transmits this to the tractor as correction information. The tractor compares and calculates the distance information received by its GNSS unit with the correction information from the base station and removes the error. This results in highly accurate position measurement with error of only a few centimeters. Kubota has independently developed an integrated RTK-GNSS unit containing receivers and other devices as a low-cost way to realize this positioning method.
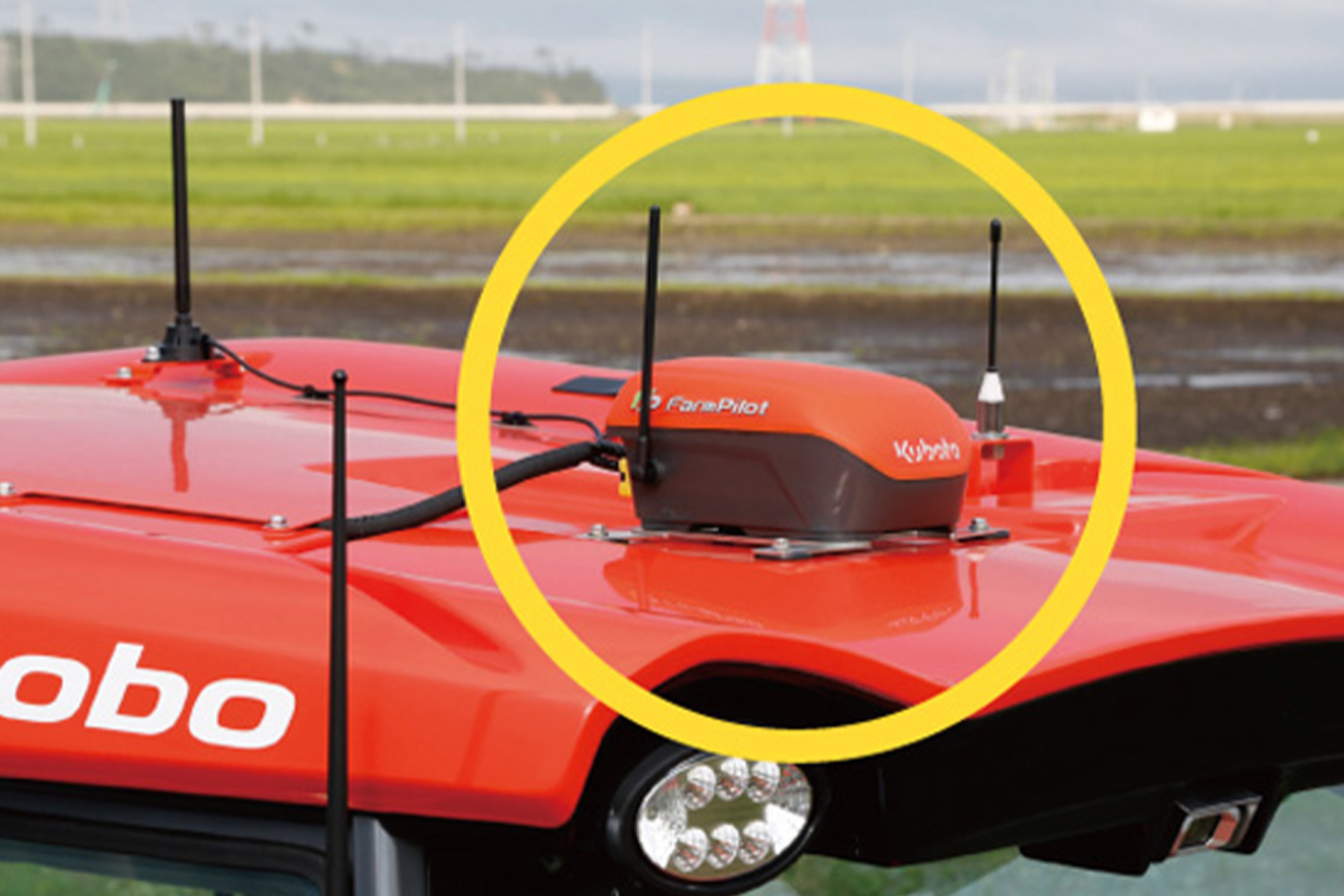
In addition, agricultural machinery works on fields with many rolls and slopes, making tilt compensation essential for measuring positions correctly and plowing the field evenly. Without tilt compensation, when the machine rides a bump and tilts to the left, the GNSS unit will also tilt to the left. This will result in a measurement of the machine with a deviation to the left compared to the correct position.
The Inertial Measurement Unit (IMU) in the RTK-GNSS unit corrects for this deviation. It compensates for the tilt of the machine from acceleration and angular velocity and accurately calculates the correct position of the machine even when it is at an angle.
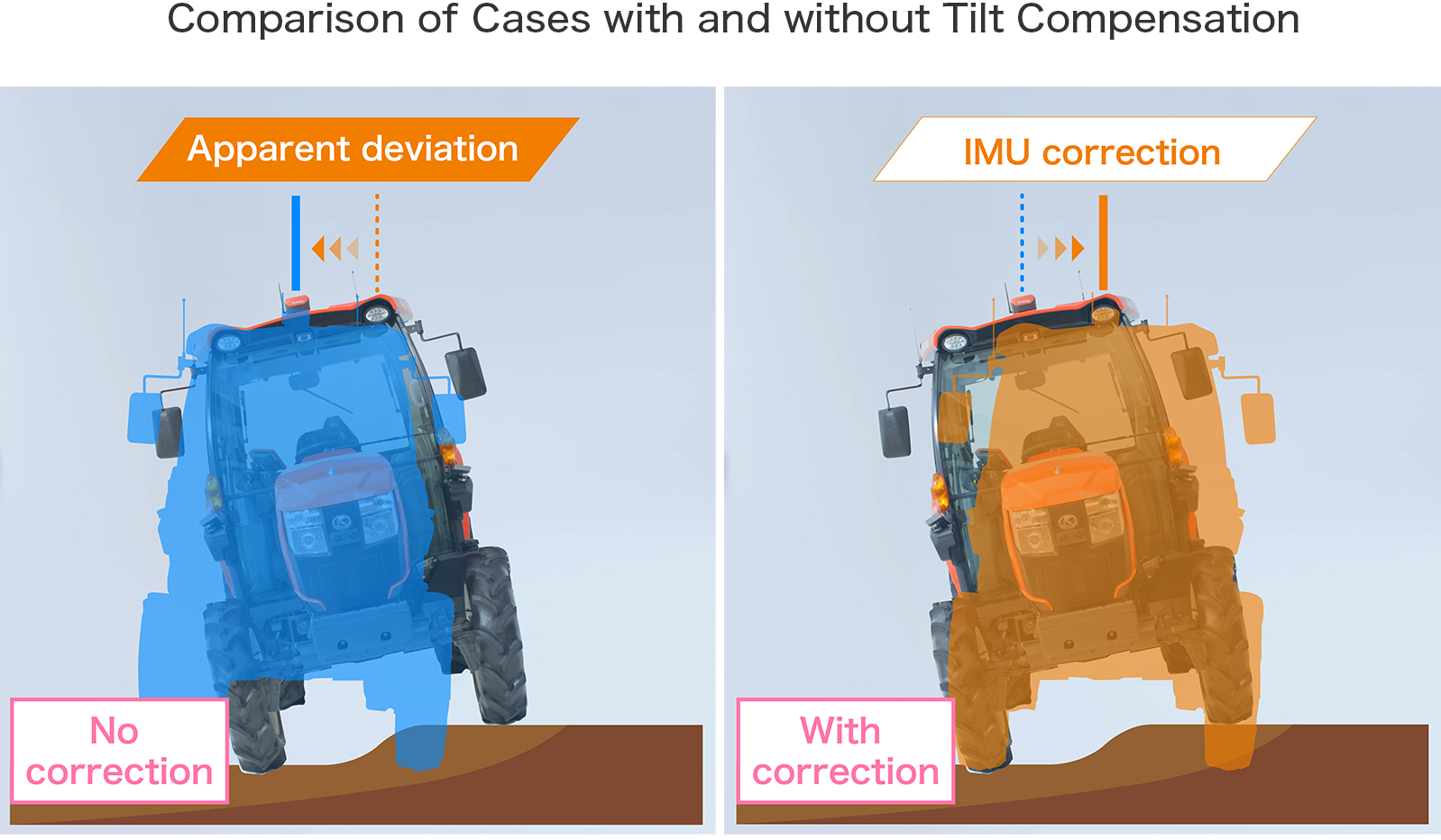
The combination of these technologies enables greater precision in automated driving with errors of only a few centimeters, even when used on uneven fields. This makes work highly precise and reduces burden on farmers, since automated driving is based on highly accurate positioning.
Surround View Enables Simultaneous Operation of Unmanned and Manned Machines
Surround View is a technology that combines images from cameras mounted on all sides of the tractor to generate a bird’s-eye view and display a clear 360-degree image of the area around the tractor. It is used to monitor surroundings during unmanned operation.

The system uses four ultra-wide-angle cameras mounted on the front, rear, left, and right sides of the tractor cabin to capture images from all directions. Software is used to convert these images into overhead views and combine them to look more natural. An image of the tractor as viewed from directly above is superimposed on the images to create the Surround View.
The Surround View image is sent wirelessly so it can be viewed on a tablet or a monitor installed in a manned machine. It ensures the safety of unmanned machinery being operated simultaneously while a farmer works with a manned machine.
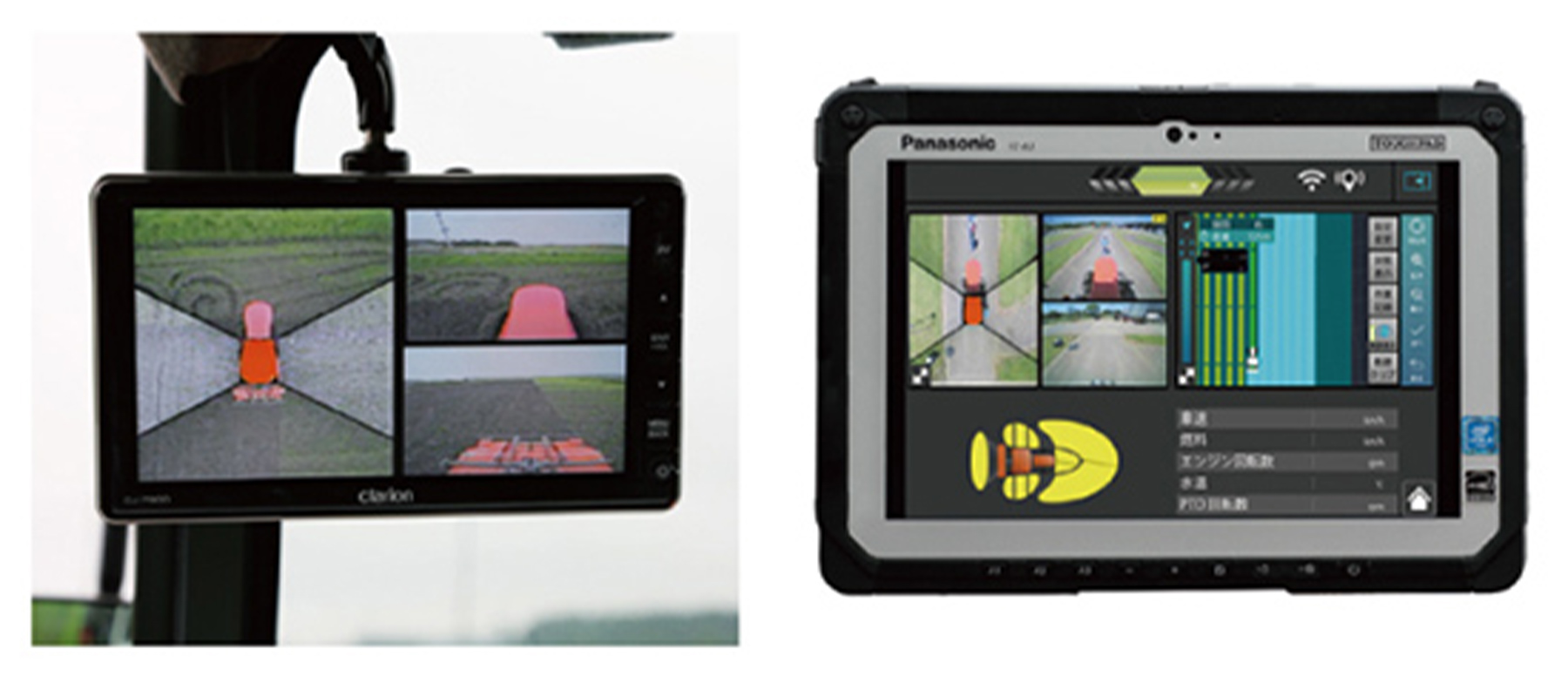
Two Types of Sensors Work Together in the Human and Obstacle Detection System
Kubota's autonomous tractor is equipped with two types of sensors – a laser scanner and an ultrasonic sonar – to detect people and obstacles around the machine.
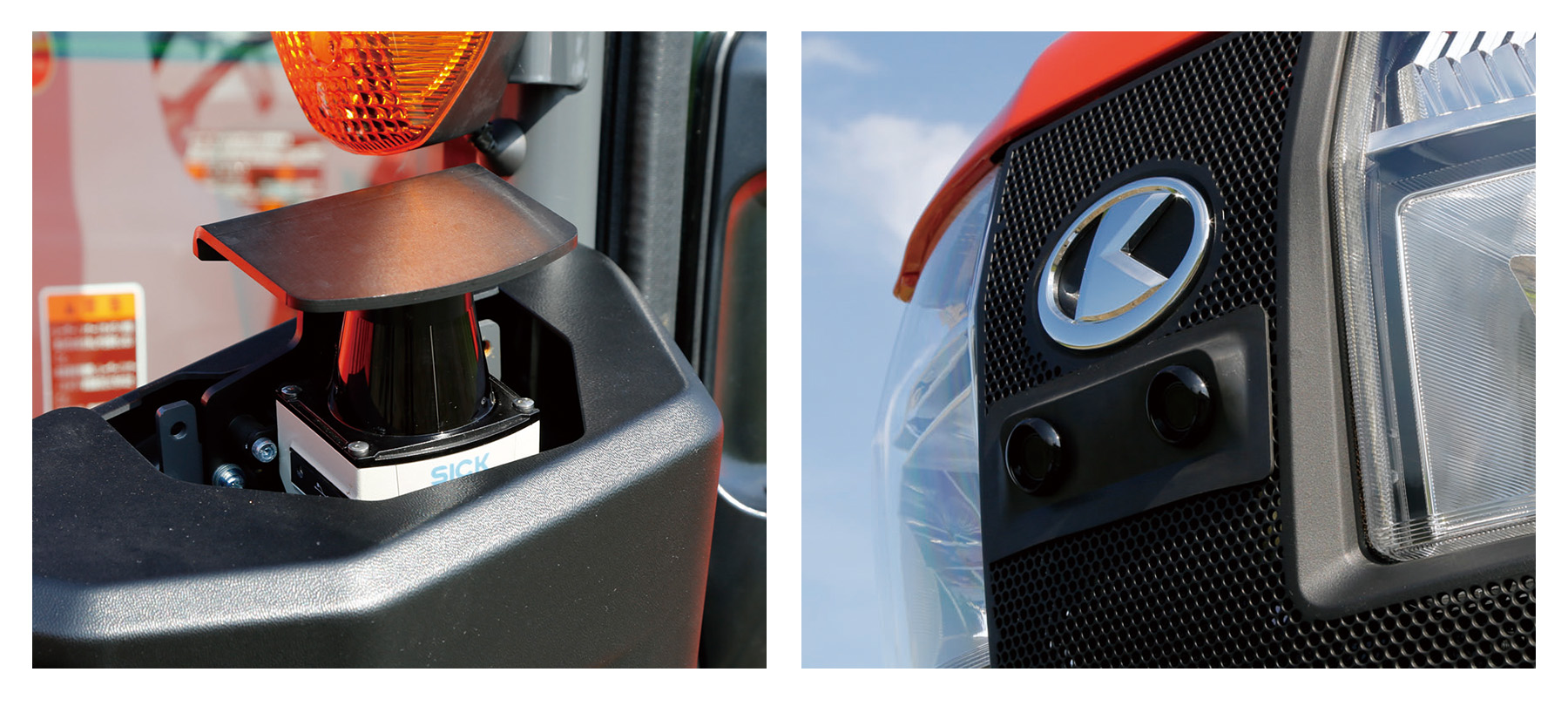
There are two laser scanners on the front left and right of the cabin, and one on the rear. These measure the distance to obstacles by firing laser beams in a wide fan shape and calculating the time required for the beams to hit the obstacle and bounce back.
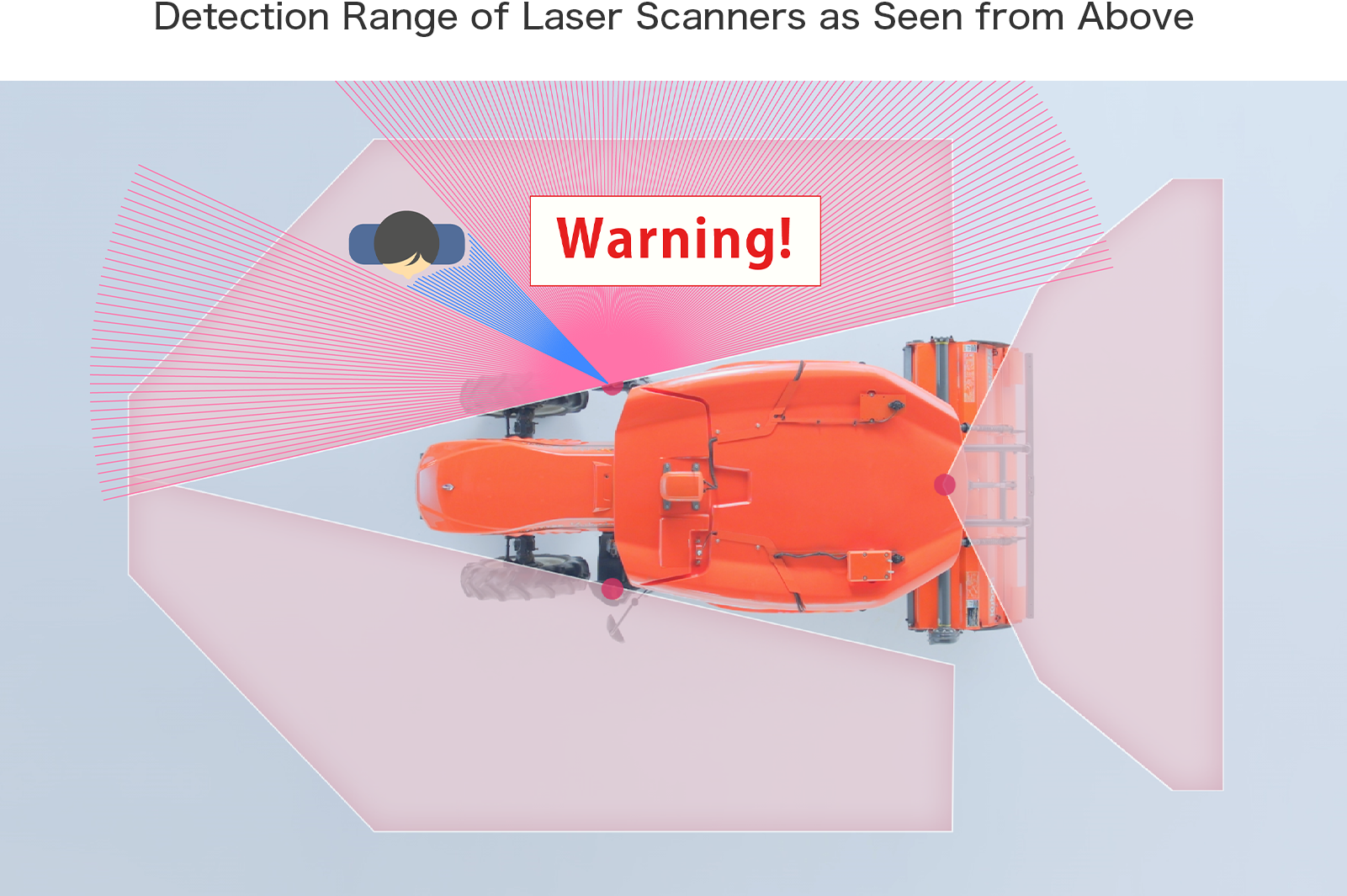
The laser beams have a far reach and are powerful for monitoring obstacles at medium to long distances. However, they are fired in a flat, fan-shaped plane, creating areas above and below the plane where obstacles cannot be detected.
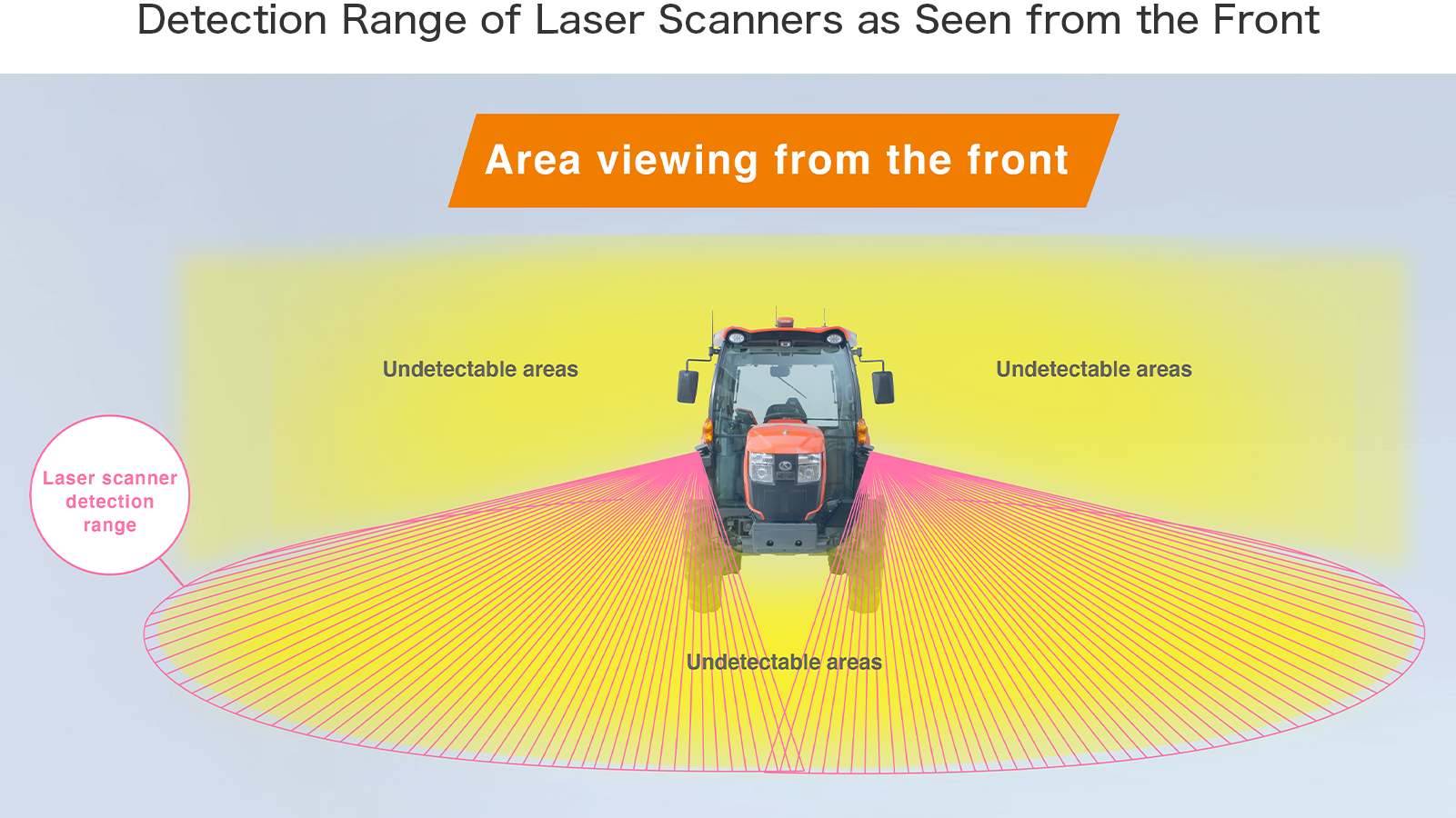
To supplement this, the system uses ultrasonic sonar units mounted on the tractor in eight places. Their ultrasonic waves spread over a wide range, including up and down, and are used mainly to detect people and obstacles at short distances.
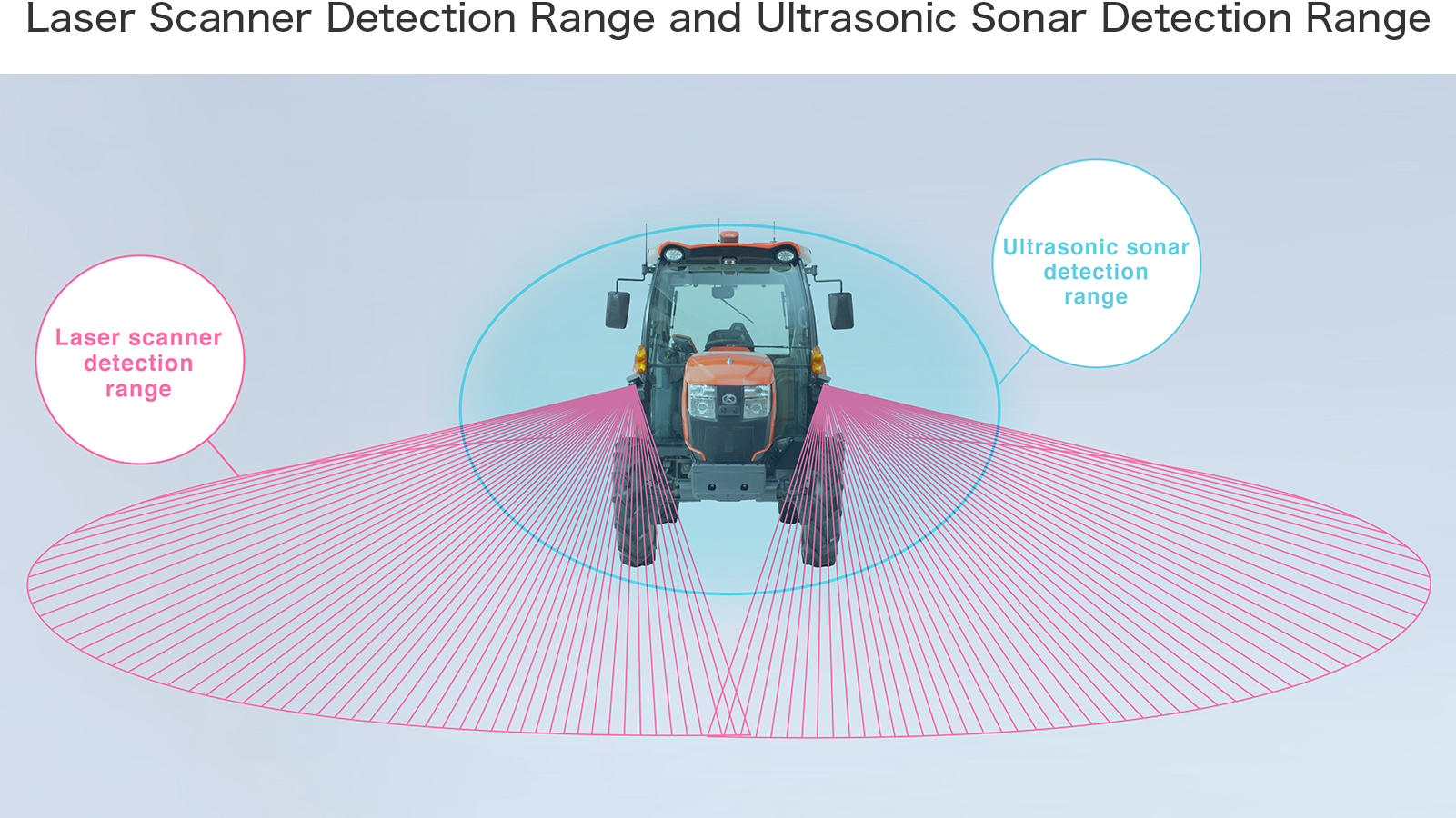
The use of two types of sensors with different operating ranges makes it possible to detect people and obstacles all around the tractor, both near and far, up and down, left and right. This allows the system to stop the tractor when obstacles are detected in the field and prevent untended starts in self-driving.
Increasing Hopes for Completely Autonomous Operation
In 2020, Kubota introduced the industry’s first self-driving rice-transplanter with auto steering in addition to a keeping straight function, which corresponds to Step 2 of its roadmap. This automated rice-transplanter newly added to the lineup comes with a voice alarm that serves as an audio guide for operation and warning points. Hopes are growing for further development of ICT and robotics technologies that will realize a fully integrated system with autonomous agricultural machinery.
What technologies will be required to realize a completely automated and unmanned system in the future?
Atsushi Shinkai of Compact Tractor Engineering Department explained as follows: “Self-driving tractors today have a variety of limitations for functional and safety reasons compared to tractors ridden by people, and they are limited in use to relatively ordinary circumstances. For self-driving agricultural machinery to become more common in the future, we need to enable such machinery to do what any ordinary machinery can do. I believe this will require development of technologies to ensure that machines can operate with stability and adequate safety even in harsh environments. A variety of technologies will be necessary for self-driving agricultural machinery to become widespread, and to ensure safety under any conditions, I think that AI camera technologies will be required.”
Farmers in Japan face a host of challenges: farm abandonment and outsourcing of work due to aging populations, dealing with shortages of labor for overseeing farm work, and improving work efficiency and reducing labor. With its self-driving automated agricultural machinery, it is clear that Kubota is working to address as many of these issues as possible so that agriculture can grow into a business with strong appeal. Kubota's self-driving agricultural machinery will be worth watching as the company continues its research and development and makes further advancements to achieve the goal of "completely unmanned operation with remote monitoring" in Step 3 of its roadmap.